Sensor:
A sensor is a device that receives and responds to a signal, which must be a form of energy such as light, heat, or a chemical reaction. When the sensor detects one or more signals, it converts them into an analog or digital representation of the input signal. This converted signal is then displayed in a human-readable format. Sensors find applications in various fields, including textile printing machines, automobiles, airplanes, data collection, monitoring systems, and other fields. In textile printing machines, sensors play a crucial role in gathering and interpreting information to enhance efficiency and functionality in different domains. Different sensors are used in textile printing machines.
Types of sensor:
Sensors can find application in numerous major sectors within the textile industry. They include:
1. electrical Sensor:
This type of sensors respond to changes in electrical properties such as voltage, current, or resistance. Examples: Photodetectors, Pressure sensors, Proximity sensors, etc.
2. Thermal Sensor:
Thermal sensors detect variations in temperature and thermal energy. Examples: Infrared sensors, Thermocouples, and Temperature sensors.
3. Chemical Sensor:
Chemical sensors identify and measure the presence of specific chemical compounds or changes in chemical properties. Examples: Gas sensors, pH sensors, and biosensors.
4. Mechanical Sensor:
Mechanical sensors respond to physical changes, movements, or forces. Examples: Accelerometers, strain gauges, and vibration sensors.
Applications of sensors in the textile sector:
Sensors can find application in numerous major sectors within the textile industry. They include:
- Yarn manufacturing sector
- Fabric manufacturing sector
- Dyeing sector
- Printing sector
- Finishing sector
- Apparel manufacturing sector
- Miscellaneous
Different types of sensors used in textile printing machine:
A textile printing machine incorporates different types of sensors. They include:
1. Crease Detector sensor:
This sensor, positioned on the print carriage of digital printers, plays a crucial role in preventing damage to print heads. When it detects a fold or seam, it automatically pauses the machine. No calibration is needed, emphasizing the importance of maintaining an evenly spread fabric without creases or protrusions.
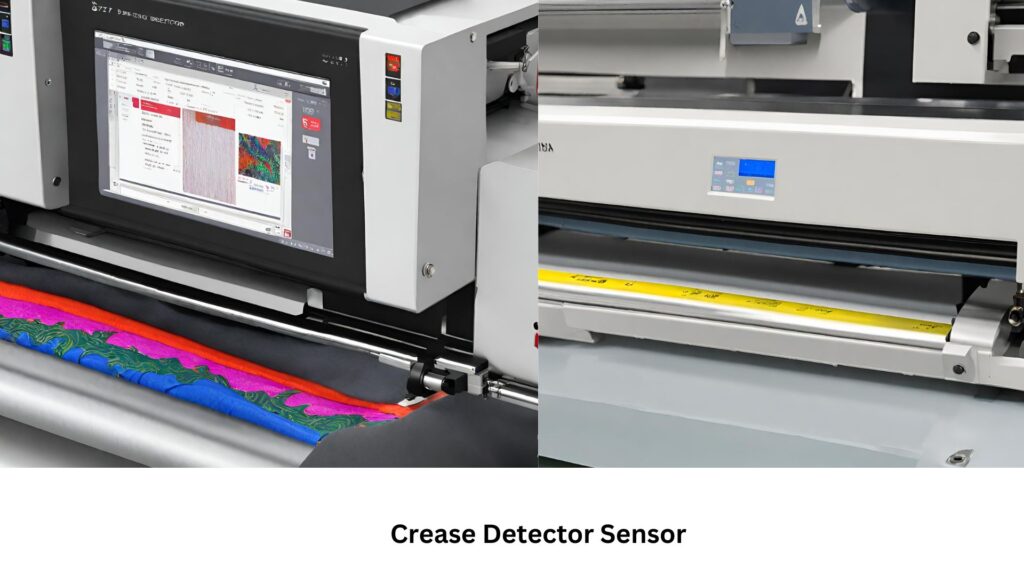
2. Fabric Detachment sensor:
Present in printers with an external dryer, this sensor, located on the fabric detachment cylinder, controls the connected dryer’s movements to prevent fabric detachment from the belt. Calibration is unnecessary, but proper fabric alignment with the belt is crucial.

3. Proximity sensor:
A device detecting the presence or absence of an object without physical contact. Used to detect the print carriage, print head, paper feed mechanism, and the presence or absence of paper, fabric, or ink in the machine.

types of Proximity Sensor:
1. Infrared Sensor:
Uses an infrared LED and a photo detector to measure reflected infrared light, detecting paper edges, fabric folds, etc.

2. Capacitive Sensor:
Utilizes an electric field to sense changes in capacitance caused by the presence or absence of a conductive material, used for detecting ink levels, paper thickness, or fabric detachment.
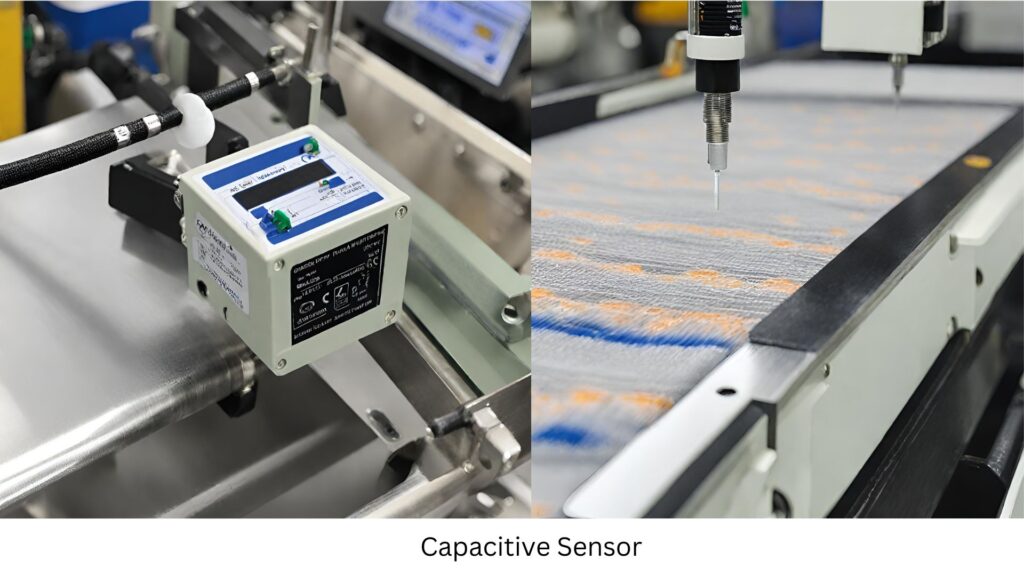
3. Inductive Sensor:
Uses an electromagnetic field to sense changes in inductance caused by the presence or absence of a metallic object, detecting metal parts that may fall into the machine.
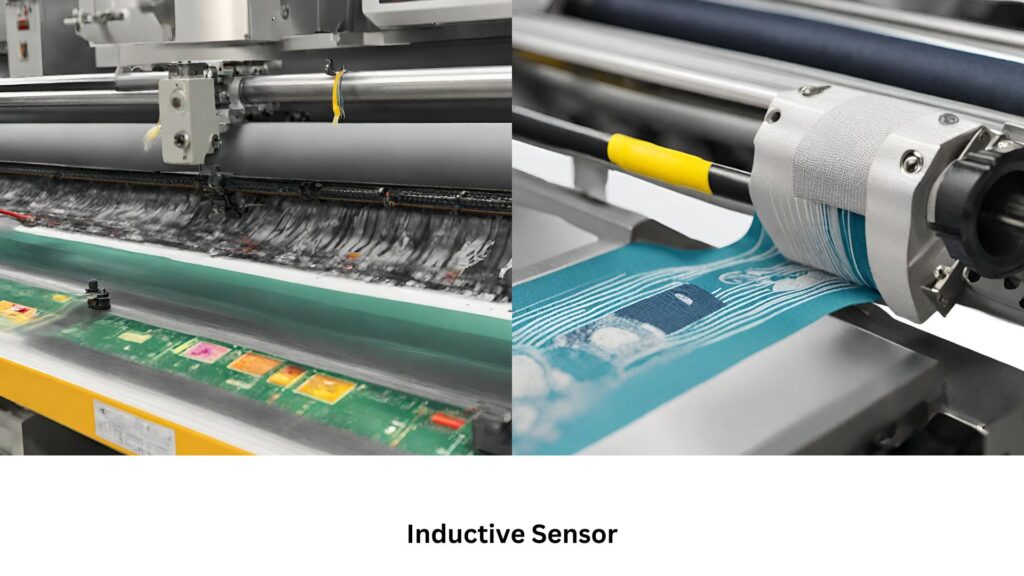
4. Fabric Positioning and Edge Alignment sensor:
Ensures accurate fabric positioning on the printing bed using sensors or mechanical guides. Edge alignment sensors, a specific type, detect the fabric or printed garment edge, aiding the printing machine control system in understanding fabric orientation accurately.
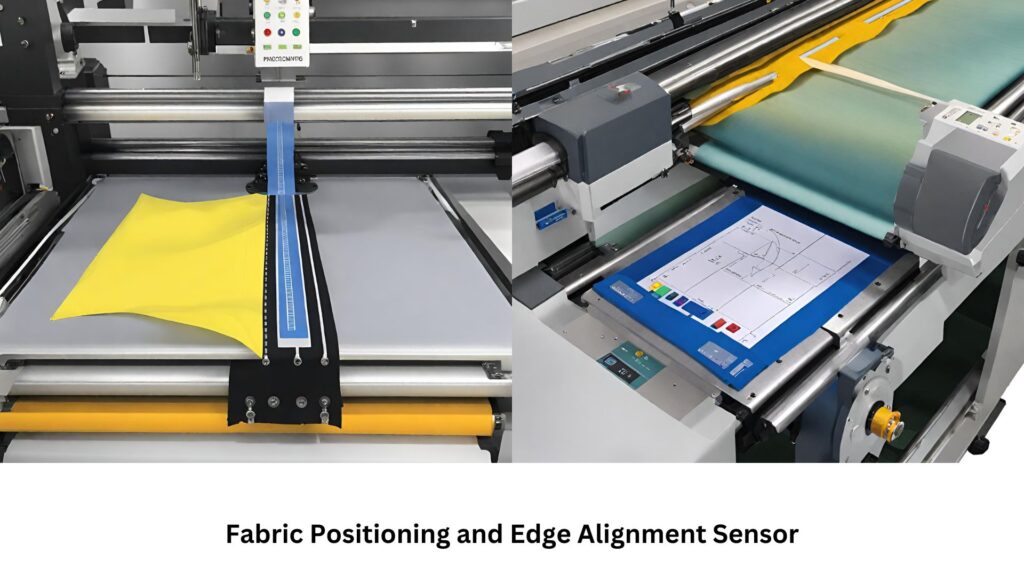
5. Printing Head Movement Detecting Sensor:
Crucial for digital printing machines, this sensor restricts print head movement to the prescribed area, ensuring error-free printing within specified boundaries by continuous monitoring and real-time adjustments.
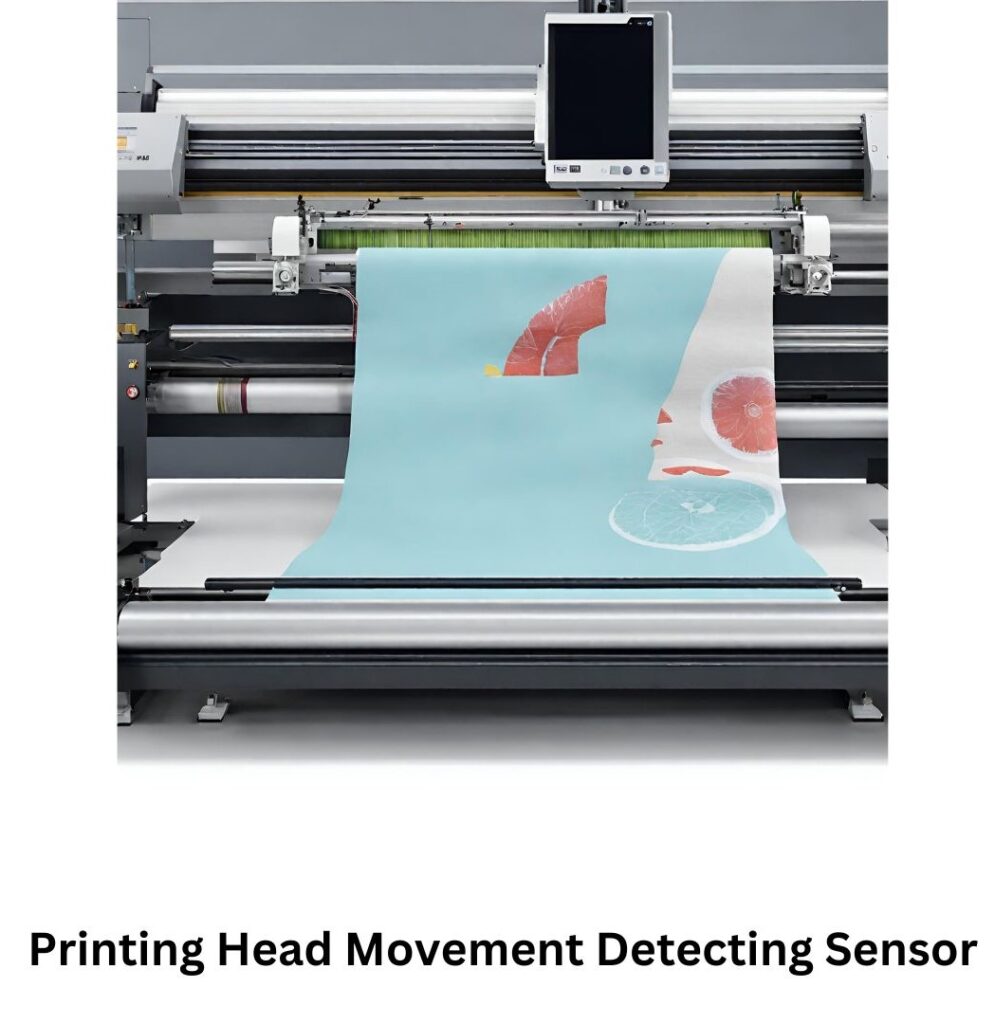
6. Speed Synchronization Sensor:
Essential for sublimation textile printing, maintains synchronization between the printing chamber blanket and drying chamber conveyor belt, preventing issues like misalignment, misprint, or fabric damage due to speed variations.

7. Laser Beam Sensor:
Acts as both a quality control mechanism and a safety device, using a modulated laser beam to detect the presence, absence, or position of paper and fabric. Allows precise detection of printing media unevenness while preventing contact with printing heads.

Major Sensors used in Octopus textile Printing Machine:
1. Color Density Sensor:
Utilizing spectrophotometers, these sensors measure the color density of the printed ink on the substrate. They analyze light reflection or transmission through the printed area. The data from these sensors is then compared to predefined color standards, ensuring the Octopus printing machine achieves the desired color density and consistency.
2. Ink Viscosity Sensor:
Viscosity sensors, also known as viscometers, actively monitor the viscosity of the ink. Recognizing the impact of ink viscosity on print quality, these sensors provide real-time feedback to the control system for maintaining the correct viscosity.
3. Web Tension Sensor:
Crucial components in the Octopus printing machine, web tension sensors play a vital role in maintaining proper tension in the material as it progresses through the printing process. Operating on the principle of measuring the force or tension applied to the web, these sensors make real-time adjustments to ensure consistent and uniform tension levels. This feedback to the control system allows the Octopus printing machine to make instantaneous adjustments, preventing issues such as wrinkling, stretching, or misalignment of the material during printing. This is essential for accurate registration and high-quality printing, while also aiding in preventing material breakage and minimizing waste.
Reference:
- Machinery of knit fabric processing by Dr. Shaikh Md. Mominul Alam and Md. Golam Kibria.
- Textile Sensors
To learn more on different textile printing machines you can check on the following article: