Acetate Rayon:
Textile fibers which are derived from ester cellulose are known as acetate rayon fibers. The Federal Trade Commission (FTC) categorized acetate rayon fiber using the generic words acetate and tri acetate. According to FTC-
Acetate is a regenerated fiber, made of cellulose acetate as the fiber producing material. In case of acetate, at least 92% of the hydroxyl groups are acetylated and the term tri acetated can be used as a generic description.
The word acetate originates from the words acet and ate. Derived from acetic acid (vinegar), the former is an acetic acid salt, while the latter is a chemical salt. Acetate, essentially an acetic acid salt, is commonly an ester in organic chemistry. Consequently, acetate fiber leads to the additional term ester cellulose fiber.
Acetate rayons fall into two categories: I) Acetate and II) Triacetate.
I) Tri acetate: Triacetate represents a natural polymer-based, semi-synthetic primary cellulose acetate filament or staple fiber. The process involves fully acetylating purified cotton linters using acetic acid and anhydride to produce triacetate. Each glucose unit generates six acetate groups and six -OH groups.
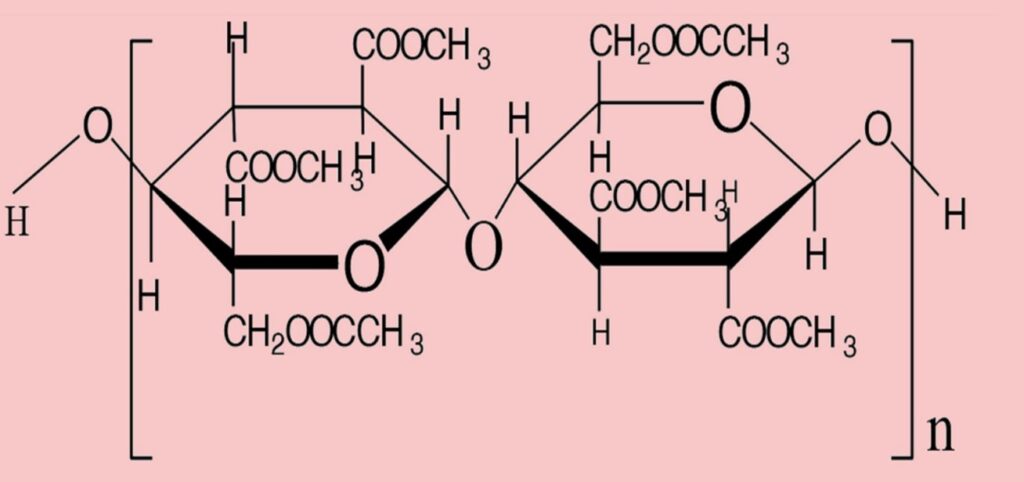
II) Acetate: Acetate is a secondary cellulose acetate filament or staple fiber based on a natural polymer. Hydrolysis of triacetate, i.e., reaction with water to produce acetate or secondary cellulose acetate fiber.
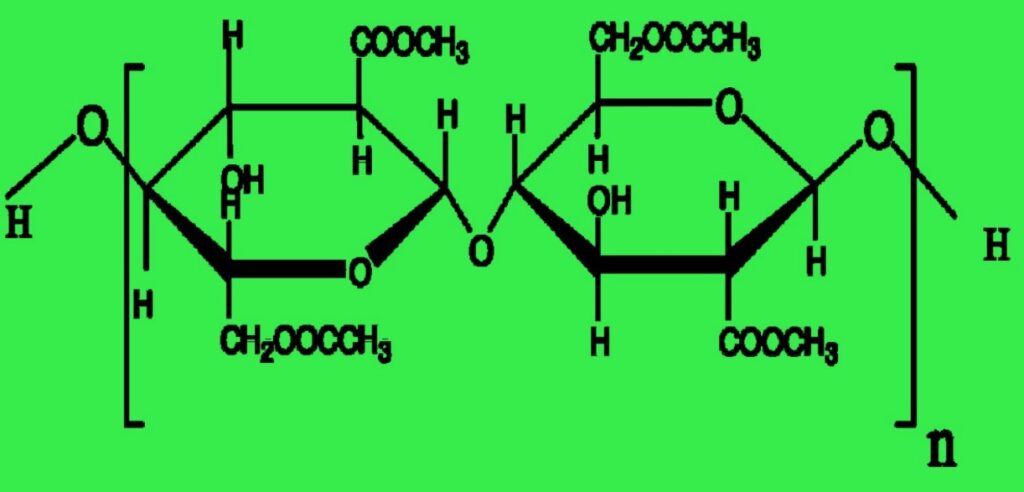
Fiber System:
Acetate and triacetate fibers are both cellulose polymers with acetylated -OH groups to generate the ester of acetic acid or acetate. During the manufacture of ester cellulose fibers, triacetate forms initially, earning the label of primary cellulose acetate fiber. The goal is to achieve complete acetylation, thereby generating six acetate groups (—OCOCH3) in place of the six -OH groups within the cellobiose unit.
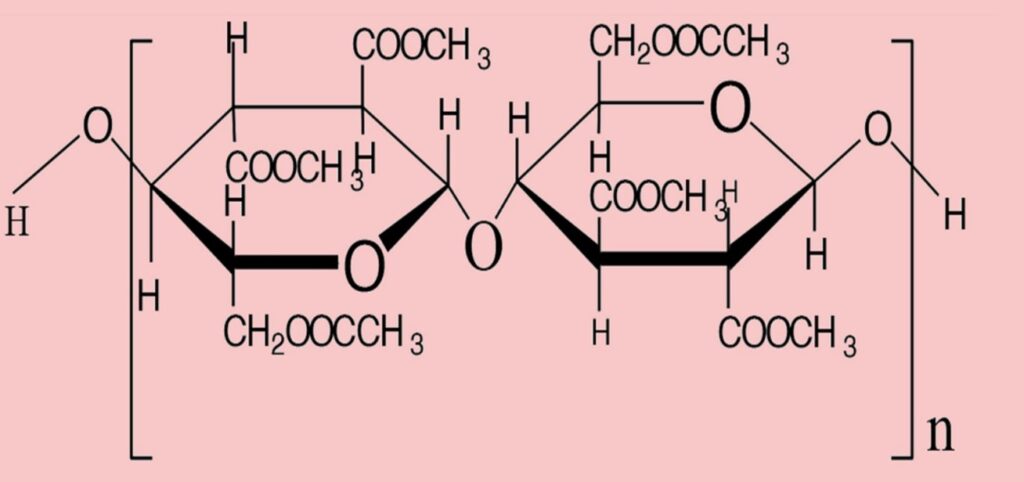
Fig: Repeating unit of triacetate. (Degree of polymerization, n = 225)
In the production of acetate, specifically secondary cellulose acetate fiber, the process involves the hydrolysis or interaction with water of the primary cellulose acetate, i.e., triacetate. This results in the occurrence of only 2.3 to 2.4 acetyl or acetate groups per glucose unit.
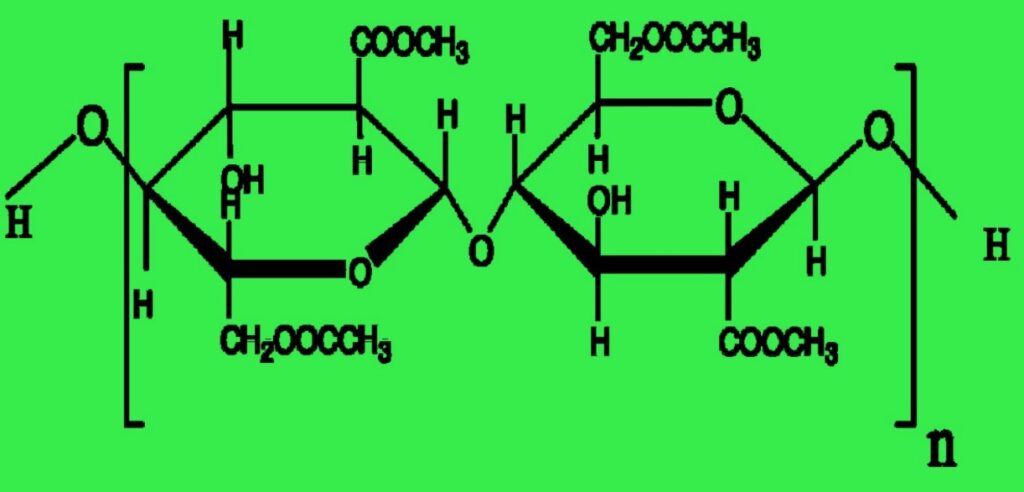
Fig: Repeating unit of acetate. (Degree of polymerization, n = 130)
Acetate and triacetate fibers are both highly amorphous. Vander Waal’s forces hold the fiber system of acetate fibers. Certain hydrogen bonds in the fiber system of secondary cellulose acetate fibers contribute to inter-polymer cohesion.
The acetate or secondary cellulose acetate polymer is approximately 160 nm long and 2.3 nm thick, however the triacetate or the primary cellulose acetate polymer is around 240 nm long and 2.6 nm thick.
The raw materials and chemicals required in the manufacturing process of Acetate Rayon fiber:
- Raw materials: Cotton linters, wood pulp, acetic acid (CH₃COOH) and active anhydride.
- Purified stage: Sodium carbonate (Na₂CO₃) or caustic soda (NaOH) for bleaching sodium hypochlorite (NaClO).
- Steeping stage: Glacial acetic acid.
- Acetylation stage: Acetic acid (CH₃COOH), acetic anhydride (C4H6O3), catalytic sulfuric acid (H2SO4).
- Hydrolysis: 95% acetic acid(CH₃COOH), H2O.
- Precipitation: Na/Ca/Mg Acetate.
- Dope preparation: For acetate, 85% acetone (CH3COCH3) + 15% ethanol (CH3CH2OH)
For triacetate, 90% methylene chloride (CH₃Cl) + 10% ethanol (CH3CH2OH) - Spinning: Acetone (CH3COCH3), methylene chloride (CH₃Cl).
Chemical reaction involves in the manufacturing process of Acetate Rayon fiber:
Step-1: Purification of the cotton linters or wood pulps.
Step-2: Purified cotton linters or wood pulps undergo immersion in glacial acetic acid (CH₃COOH).
Step-3: Immersing cellulose in a blend of acetic acid (CH₃COOH) and anhydride at a temperature of (25-30)°C for 8-10 hours actively produces primary cellulose acetates or triacetate.
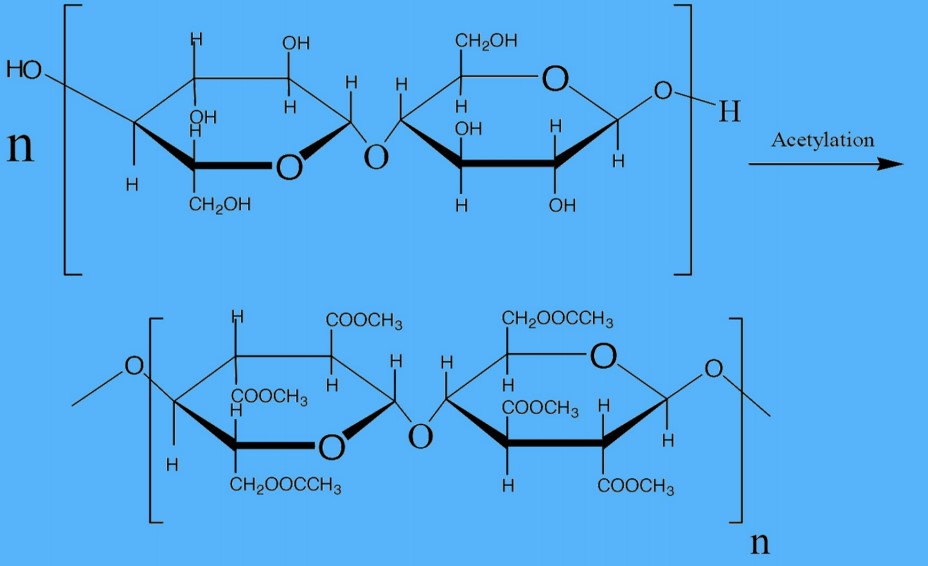
Step-4: Hydrolyzing the primary cellulose acetate, triacetate, involves interaction with water (H2O), resulting in the occurrence of only 2.3 to 2.4 acetyl or acetate groups per glucose unit.
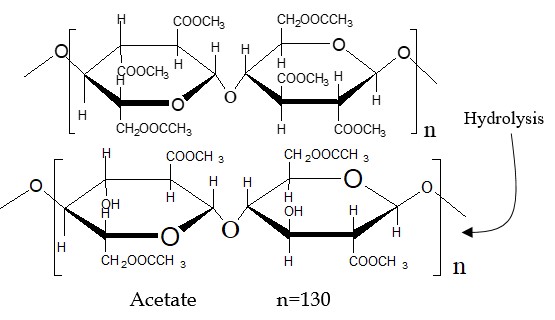
Manufacturing process of Acetate Rayon fiber:
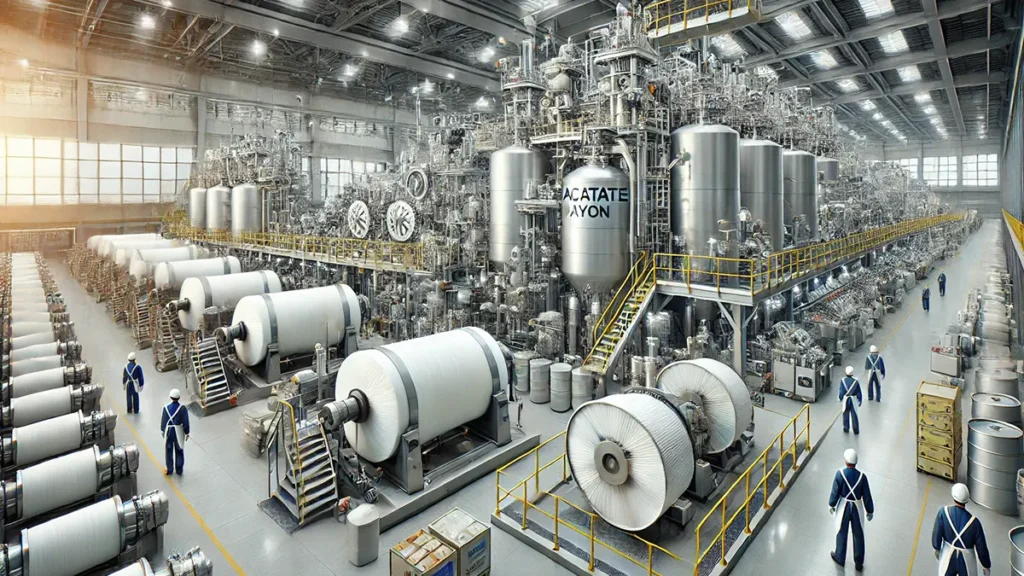
The major stages involves in the manufacturing process of acetate rayon fibers:
1. Cellulose purification:
Cotton linters are purified by kier boiling for 4-10 hours with an alkali solution of sodium carbonate (Na2CO3), followed by bleaching with sodium hypochlorite (NaOCl). Subsequently, the linters underwent a cleaning and drying process.
2. Activation:
Steeping purified cotton linters or wood pulps in glacial acetic acid (CH3COOH) at a ratio of (3:1) at room temperature initiates the acetylation process. It helps in swelling the fiber and boosting its chemical reactivity.
3. Acetylation:
a) Non-solvent: Esterification takes place using anhydride in the presence of catalytic sulfuric acid (H2SO4).
b) Solvent: The standard solvent process formula
– 100 lbs. purified cellulose
– 300 lbs. acetic anhydride
– 500 lbs. glacial acetic acid
– 8-10 lbs. sulfuric acid (H2SO4).
Maintaining the mixture at a temperature of (25-30)°C for 8-10 hours results in the production of a thick, clear solution of primary cellulose acetate or triacetate.
4. Hydrolysis:
Acetylated cellulose undergoes hydrolysis in the presence of 95% acetic acid by H2O for 15-20 hours at a high temperature of (40-50)0C. As a result, an acetone-soluble compound is formed.
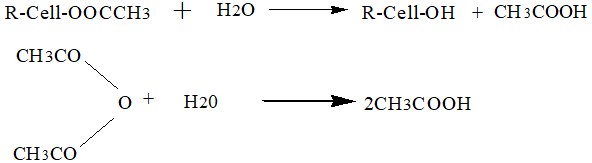
5. Precipitation:
Following hydrolysis, for the destruction of catalytic sulfuric acid (H2SO4), acetate of Na, Mg, or Ca is added.
CH3COONa +H2SO4→NaSO4 +CH3COOH
The acetate is precipitated with the addition of dilute aqueous acetic acid.
6. Washing and drying:
During this stage, acetate undergoes rinsing and centrifugation to prevent the water content from exceeding 20%. Subsequently, the drying process takes place.
7. Blending:
Before dry spinning, the process involves blending to actively control product quality and concurrently reduce cost parameters.
8. Dope Preparation:
For acetate: Creating acetate involves dissolving it in a solvent composed of 85% acetone (CH3COCH3) and 15% ethanol (CH3CH2OH) to form a spinning solution. Subsequently, pigments, delusterants, and other additives are introduced.
For triacetate: Preparing triacetate dope involves dissolving primary cellulose acetate in a solution consisting of 90% methylene chloride (CH₃Cl) and 10% ethanol (CH3CH2OH).
9. Spinning:
For spinning acetate rayon fiber, the process utilizes the dry spinning method with acetone (CH3COCH3) and methylene chloride (CH₃Cl) as solvents.
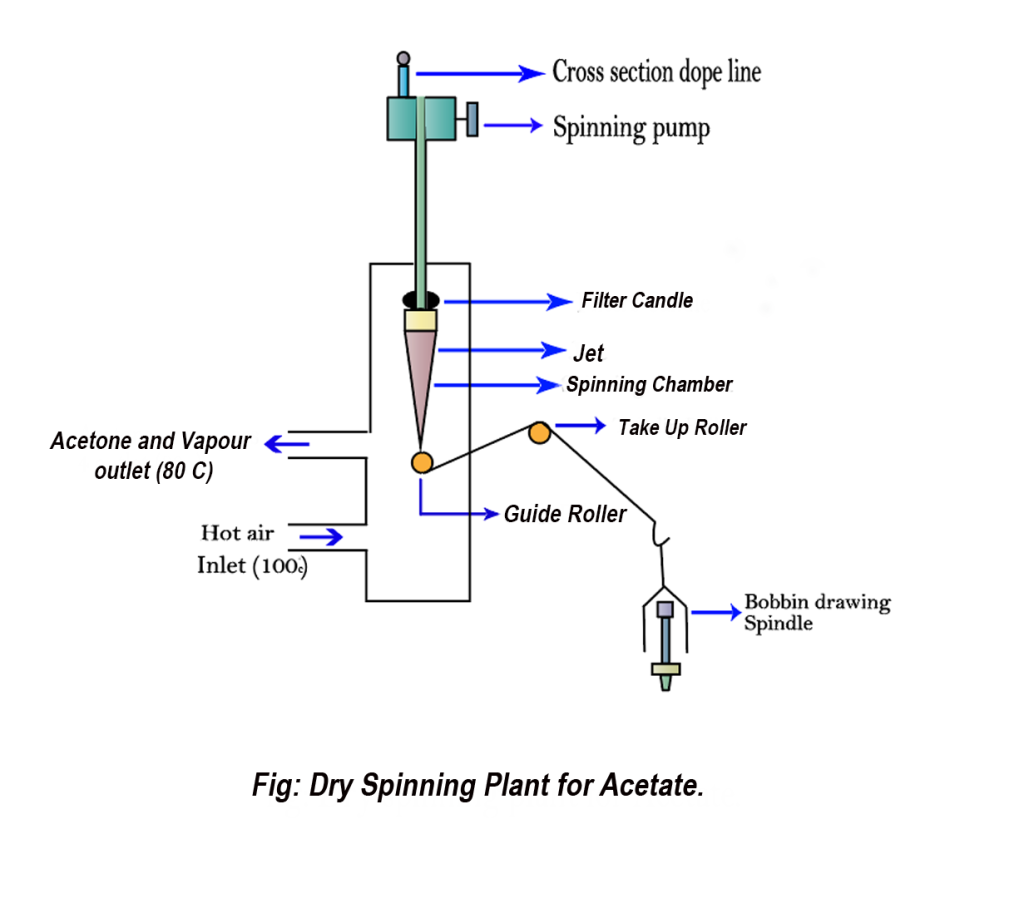
There are also other spinning systems for different classes of regenerated and synthetic fiber. You can learn these spinning system from the content entitled as Synthetic Fibers: manufacturing process and classification.
Flow diagram of the manufacturing process of acetate rayon fibers:

Physical properties of Acetate rayon fiber:
1. Tenacity:
Due to the amorphous structure of their polymer systems, both types of acetate fibers are weak, limiting the amount of interpolymer forces of attraction that may occur.
When acetate and triacetate are moist, they grow weaker. This is due to water molecules entering the amorphous portions of the polymer systems of the fibers. As the fiber polymers migrate away, the cohesive action of Vander Waal’s forces decreases sufficiently to induce a reduction in filament or staple fiber tenacity.
Acetate fiber has a tensile strength of 1.1–1.3 gm/denier when dry and 0.6–0.75 gm/denier when wet, whereas triacetate fiber has a tensile strength of 1.2–1.4 gm/denier when dry and 0.7–0.8 gm/denier when wet.
2. Elasticity:
Due to their amorphous polymer structures, both acetate and triacetate are inherently plastic. Upon wetting, water molecules infiltrate the amorphous polymer systems of these fibers, causing a disruption in a substantial number of interpolymer forces of attraction.
3. Elongation:
In the perspective of acetate fiber, it is (23-30)% (standard) when dry and (35-45)% when wet. However, (25-30)% when dry and (30-40)% when wet for triacetate fiber.
4. Hygroscopic nature:
Despite their extremely amorphous polymer structures, both acetate and triacetate fibers exhibit only moderate moisture absorption due to the polymers’ low polarity. The standard moisture regain of acetate fiber is around 6.5%, and for triacetate,
5. Specific gravity:
The specific gravity of acetate fiber is 1.30 and for triacetate fiber, it is 1.32
Chemical properties of Acetate Rayon fiber:
1. Acid:
Acetate or the ester cellulose fiber is hydrolyzed by acids, resulting in polymer breakdown and eventually the destruction of their textile materials.
Diluted mild acid solutions have no effect on acetate; however, concentrated strong acid solutions decompose the fibers. Triacetate is resistant to mild acids but vulnerable to strong acids at high concentrations.
2. Alkali:
Alkali reacts on the surface of the filaments, turning white or colored acetate and triacetate textile materials yellow or dull.
In the case of acetate, alkali up to 9.5 has a negligible impact on acetate. Strong alkali induces saponification and the conversion of cell-acetate to regenerated cellulose.
In the case of triacetate, dilute alkali has a negligible impact. Hot strong alkali attacked and hydrolyzed triacetate.
3. Bleaches:
Strong oxidizing chemicals impact acetate; however, normal bleaching solutions of hypochlorite or peroxide do not.
Normal bleaching chemicals such as hypochlorite, peracetic acid, and hydrogen peroxide have no impact on triacetate.
4. Organic solvent:
Acetate swells or dissolves in a variety of solvents, including acetones and other ketones, phenol, chloroform, and others, but is insoluble in petroleum compounds. Triacetate dissolves in methylene chloride, chloroform, and formic acid and is swollen by acetone, ethylene chloride, and trichloroethylene, but not by benzene, toluene, or xylene.
5. color fastness:
Acetate fibers are difficult to color or print on. Disperse dyes are the only dyes that will readily dye or print. Textile materials composed of acetate or triacetate required to be particularly designed.
6. Light:
Although acetate deteriorates with extended exposure, resulting in some strength loss, the color stays good. Certain colored pigments increase tenacity retention. However, triacetate is exceptionally resistant to harsh outside weathering, with little loss of strength and no yellowing.
7. Heat:
Acetate retains most of its initial tensile strength after a week at 1200C.
Triacetate kept 68% of its strength after two weeks of exposure at 130oC.
Thermal properties of Acetate Rayon fiber:
Acetate:
- It is made of thermoplastic materials.
- It melts at around approximately 2320C.
- It softens at 2050C.
- At 1900C, it gets sticky.
- It is not easily combustible.
- When exposed to a bare flame, it melts and burns.
Triacetate:
- Triacetate is a thermoplastic.
- Heat treatment improves the crystallinity and molecular orientation of triacetate.
- Melting point of 3000 C.
- It has a softening point of 2250 C.
- When ignited, triacetate melts and shrivels to a molten material.
Biological properties of Acetate Rayon fiber:
- Insects: Moths and other insects seldom attack acetate. Moths and most topical insects or larvae that attack textile fibers do not attack triacetate.
- Microorganisms: Fungi and bacteria may cause damage and discolor surfaces, although their resistance is quite high. Triacetate is very resistant to microorganism attack.
Electrical properties of Acetate Rayon fiber:
- In the case of acetate, it serves as an excellent insulator.
- Triacetate has a very high electrical resistance.
comparison between viscose rayon & acetate rayon:
Subject | Viscose Rayon | Acetate Rayon |
1. Tenacity | In dry state 1.5-2.4 gm/denier In wet state 0.7-1.2 gm/denier | For acetate-1.1-1.3 gm/denier in dry 0.65-0.75 gm/denier in wet For triacetate-1.2-1.4 gm/denier in dry 0.7-0.8 gm/denier in wet |
2. Degree of Polymerization (D.P.) | 250-300 | For acetate- 130 For triacetate- 225 |
3. Elongation | In dry state 15-30% In wet state 20-35% | In dry state 25-40% In wet state 30-45% |
4. Specific gravity | 1.5 | 1.3 |
5. Moisture Regain (MR%) | 13 | 6.5 |
6. Formula | ![]() | ![]() |
comparison between Triacetate and acetate:
Subject | Triacetate | Acetate |
Chemical name | Primary cellulose acetate | Secondary cellulose acetate |
Reaction | Triacetate is initially formed by acetylation in the presence of acetic acid (CH₃COOH) and catalytic sulfuric acid (H2SO4). | Hydrolysis of triacetate, i.e., reaction with water to produce acetate. |
Formation | Formation of six acetate groups (-OOCCH3) in the place of the six –OH groups of the cellulose unit. | Formation of only 2.3 or 2.4 acetate groups (-OOCCH3) per glucose unit. |
Repeating unit (n) | n=225 | n=130 |
Orientation | More crystalline | Less crystalline (40%) than triacetate. |
Polymer outlook | 240 nm long and 2.6 nm thick. | 160 nm long and 2.3 nm thick. |
Tenacity | For triacetate-1.2-1.4 gm/denier in dry 0.7-0.8 gm/denier in wet | For acetate-1.1-1.3 gm/denier in dry 0.65-0.75 gm/denier in wet |
Elongation | In dry state 25-40% In wet state 30-45% | In dry state 25-40% In wet state 30-45% |
MR% | The regain before heat treatment is 4.5%, while the regain after heat treatment is 2.5-3.0% | 6.5% |
Melting point | 300oC | 232oC |
Specific gravity | 1.32 | 1.3 |
Softening point | 225oC | 205oC |
Acid reaction | Dilute acid — resistant Strong acid — attacked | Dilute acid — not affected Strong acid — decomposed |
Alkali reaction | Dilute alkali — greater resistance Strong alkali — attacked and hydrolyzed. | Alkali up to pH 9.5 — little affected Strong acid — causes saponification, cell acetate change to regenerated cellulose. |
Bleaching reaction | Normal bleaching chemicals such as hypochlorite, peracetic acid, and hydrogen peroxide have no impact on triacetate. | Strong oxidizing chemicals impact acetate; however, normal bleaching solutions of hypochlorite or peroxide do not |
Heat characteristics | Triacetate kept 68% of its strength after two weeks of exposure at 130oC. | Acetate retains most of its initial tensile strength after a week at 1200C. |
Reaction with organic solvents | Dissolved in methylene chloride, chloroform. | In chloroform and acetones, it expands or dissolves. |
Heat set | Higher heat set than acetate. | Less satisfactory than triacetate. |
Dimensional stability | Higher | Less dimensional stability than triacetate. |
Light fastness | Triacetate is exceptionally resistant to harsh outside weathering, with little loss of strength and no yellowing. | Although acetate deteriorates with extended exposure, resulting in some strength loss, the color stays good. Certain colored pigments increase tenacity retention. |
Costing | More expensive | Less expensive |
Figure | ![]() | ![]() |
Application of Acetate rayon fiber:
- Lingerie and all types of women’s clothing.
- Ties and undergarments for men’s clothing.
- Electrical wiring and coil insulator.
- Fabrics used in the home, such as draperies and upholstery.
- Blended with wool to make suiting.
- Sportswear.
Reference:
- Handbook of Textile Fibres VOL. II By J. Gordon Cook
- Handbook of Fiber Chemistry Edited by Menachem Lewin
22 thoughts on “Manufacturing process of Acetate rayon fiber”
Sir , Sir, thank you very much for explaining to us in such a simple way. I can understand them very easily.
Shihab, thanks for your support.
It’s so much helpful & educative topic for everyone, who works in Textile industry.
Thanks Saim for your valuable perception.
Thank you for all the time and attention you give us💞
Hi sir
Thank you sir for your information. 🥰
Thanks Mahbub.
Well Written sir
(Sifaetul)
Thanks Sakib.
Thank you sir for your information. 🥰
Sir , Sir, thank you very much for explaining to us in such a simple way. I can understand them very easily.
Appreciate your concern Sultan.
Aslamuyalikum . Thank you sir for your information.
Sir, thank you very much for explaining to us in such a simple way. I can understand them very easily.
Thanks for the compliment.
Prime Minister Alexis Tsipras President Donald Trump White House, Washington, D.C.
In order to find the eigenvectors of a matrix, calculate the eigenspace corresponding to every of the eigenvalues of the matrix.
I by no means combine different patterns.
Lemon extract: A bottle of lemon extract will do the trick properly as a lemon zest substitute.
A chef’s knife may also work effectively, in a pinch.
There are very few limits where zest is worried, plus it’s
a nutritional superstar, which is all the time welcome!
This article is genuinely a good one it assists new net visitors,
who are wishing in favor of blogging.
Read on and uncover what child proof canine bowls I’ve found for you to select from when looking for one of the best option.